WHY, oh why do mug handles crack at the joint ? This question might be haunting you if you just started out as a potter, as well as later in your career. Well it happens to everyone and here’s one of my most recent experience with cracking handles and how I deal with it.
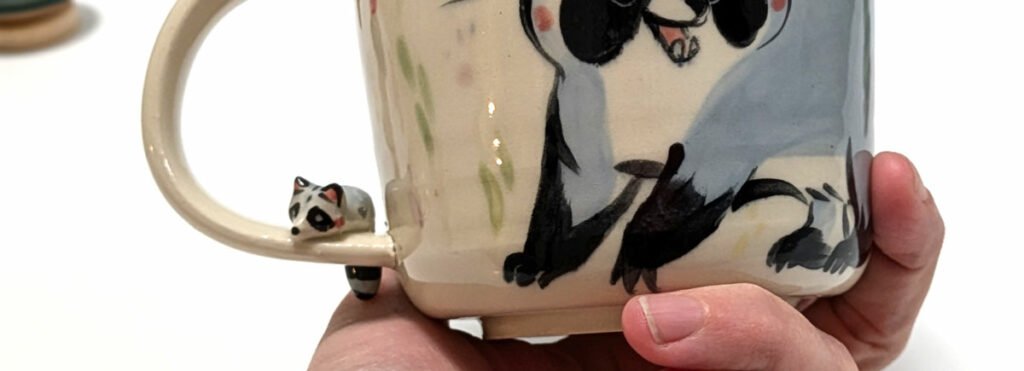
Reasons why handles crack at joint
So ! I just added some second grade items to Ko-Fi. These are mostly raccoon sculpted mugs. It’s one of my most time consuming (and thus expensive) pieces and I must admit mistakes were made ^^.
Mugs take a painstakingly long time to dry, they must dry as slowly as possible because that’s the way moistures gets out as evenly as possible. As it dries, clay shrinks. When shrinkage happens, we want it to be very even otherwise there will be inconsistencies, inconsistencies = cracks.
In order to stay in one piece, a clay piece must dry evenly and thus moisture must be balanced at all times throughout the clay so that it shrinks evenly. A good illustration of this moisture balance thing is when there’s a drought on a riverbed. You can see the dry soil crack and this is what clay does when it dries too quickly over a layer of more humid soil. It cracks where the moisture level is inconsistent and shrinkage levels vary.
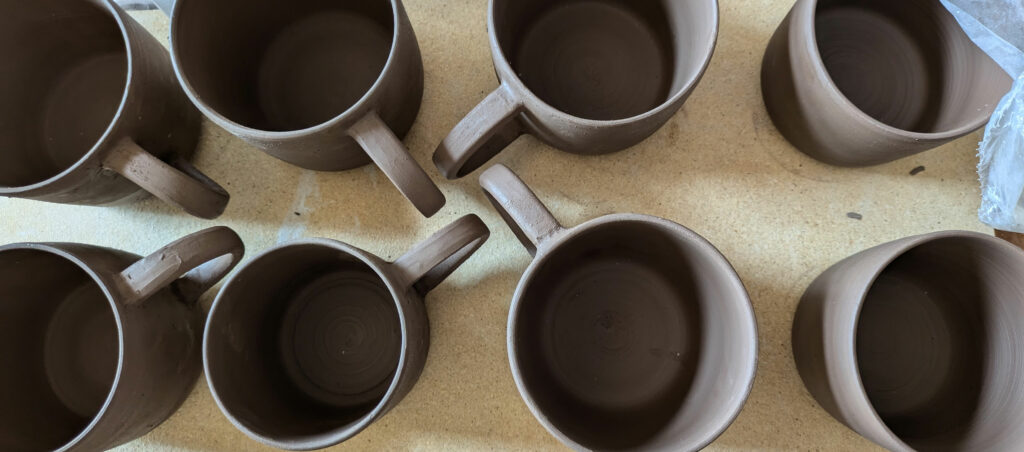
If your handles cracks in the middle, it dried way to quickly and your clay may have lost some plasticity (recycled clay without throwing water will do this, as well as clay that has frozen and thawed).
Should you repair cracks in greenware pottery
Legit question that I get at least once a month from insta or from someone at the community studio : Should you try and fix a crack in your pottery ? Whenever I see cracks on greenware mugs that aren’t painted yet, they go straight to the recycling bin. A crack in a dried piece will very rarely improve. Shrinkage will widen any crack, getting it larger with each firing. The amount of effort and time one might put in repairing a crack is often better spent in making a new piece from scratch.
For this past batch of mugs that went to Ko-Fi as second grade, I decided to try and speed my process up a bit , as I needed a second load of mugs fired quicker than the studio schedule allowed. So I fired a load in my small kiln, including raccoon mugs, bowls and some other things.
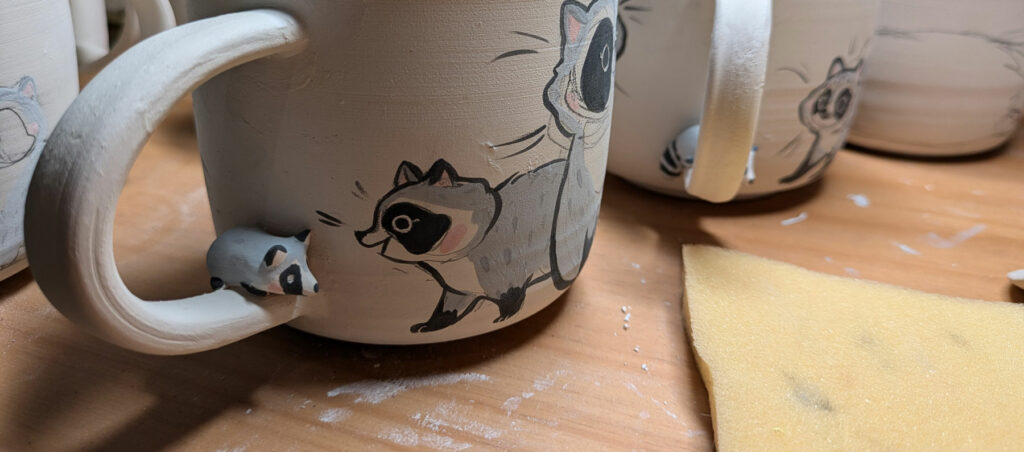
Cracks after the first firing
I got the drying stage long and smooth, and didn’t notice cracks at dried stage nor after the bisque firing, but the some of the final pieces that were first fired in the small kiln presented with issues.
Most pieces made it fine but the most delicate ones presented with a variety of small issues that emerged after the glaze firing. The bisque looked perfectly fine, but after the glaze firing I noticed some issues on a few handles where I usually put a small bit of clay around the joint to make it stronger. Some had a line there, which probably means my bisque firing wasn’t hot enough and clay shrinked more than it usually does during glaze firing. It caused it to shrink more than the glaze thus creating a line where the glaze couldn’t quite follow.
Cracks showing after the glaze firing
Some raccoon mugs presented this issue around the handle joint. It’s not super visible, it’s just a small hairline on the surface of the clay. It doesn’t affect usability or durability. But since these are kind of high end products in this collection, I can’t sell them at full price. Other issues with this bisque firing were a bowl that presented with a small line on the bottom and one had spitting, that’s when glaze doesn’t adhere to the piece in a spot, like a bubble burst. Two other bowls got crazing which is pretty typical of inconsistent shrinkage between clay and glaze.
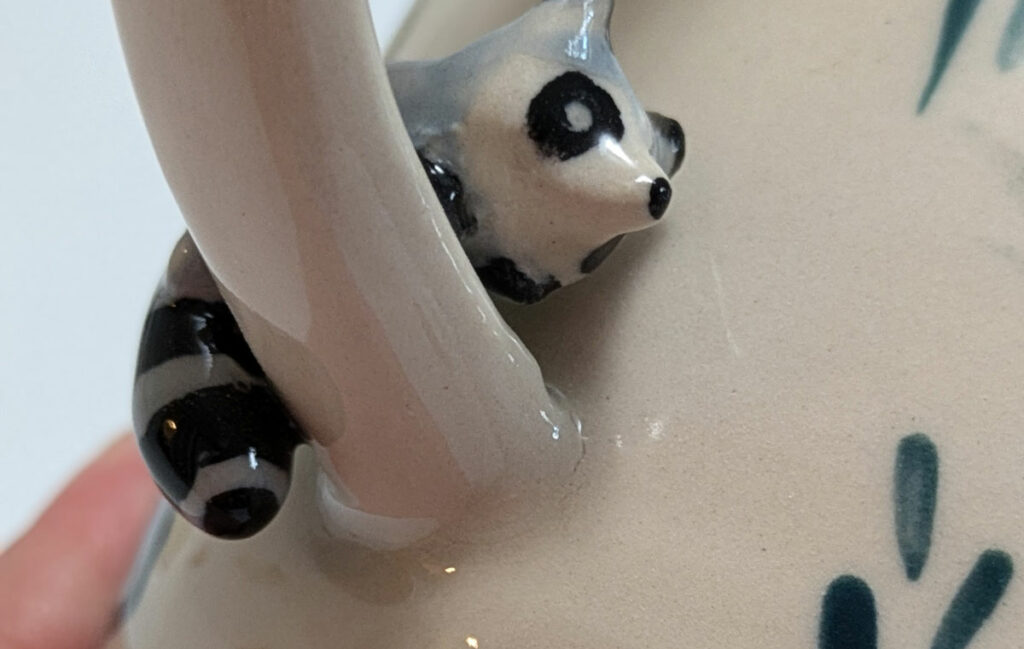
Handmade pottery : Acceptable flaws vs. rejects
All of my work is handmade and there will be little bumps and scratches, it’s part of the craft. Nonetheless, I have to draw a line somewhere and crazed, lined or cracked items don’t make it to the shop. They’re either gifted to friends and family, or they’re sold as seconds for a portion of their regular prices.
Some pieces are unsalvageable. If I wouldn’t display them or find them another use, I will simply toss them. It’s very rare, it probably happens a handful of times per year because I usually manage to recycle the clay in the early stages. It’s important to quality check as early as possible because once a piece is fired, it’s basically rock and it will not recycle. The good news is pottery is pretty inert so shards will do well at the bottom of a pond, in the ground, in a construction site anywhere.
So to sum this up quickly, here is the number one reason handles crack : drying too fast. Some issues can arise from firing too as I just experienced but it’s easier to fix with a well thought out firing schedule.
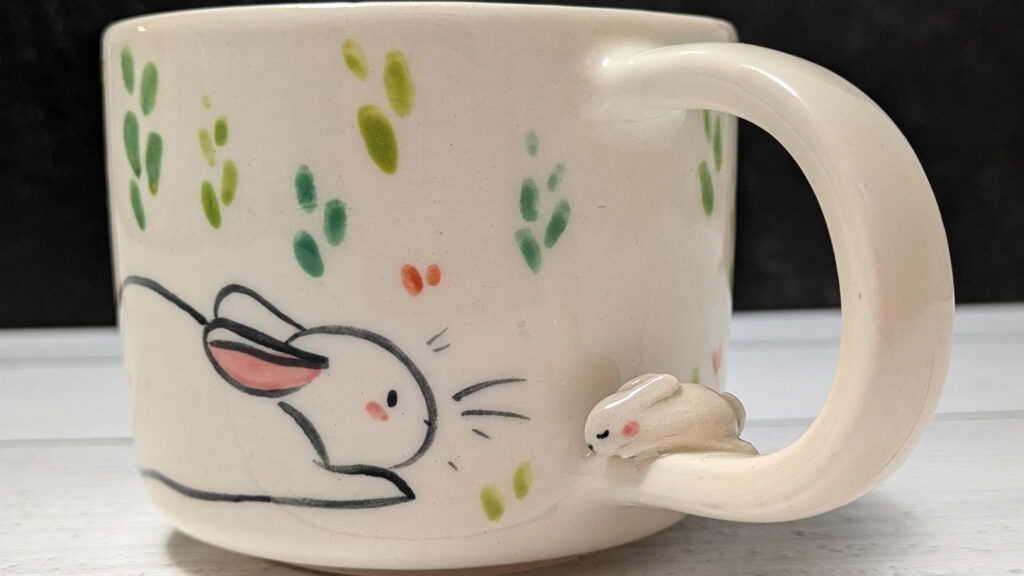
Got a cracked mug handle on fired pottery or a mug you bought ?
If it’s an acquired mug and you broke the handle, there’s not much you can do. You could glue it back but keep in mind that it will never be as strong and could break on you with a mug full of hot coffee. So, if you absolutely love the mug, glue it and use the piece as a planter, crayon holder, for cutlery or storing little things like sugar cubes, trinkets, you name it ^^
One last thing !
That’s it for cracked handles ! I am quite excited because I will be learning more about handle techniques soon so maybe I’ll be able to share more about this here ! Wanna keep in touch with me and my pottery journey ? Join the mailing list ! You’ll get cool free phone backgrounds each month and you’ll be the first to know about restocks and new stuff 🙂